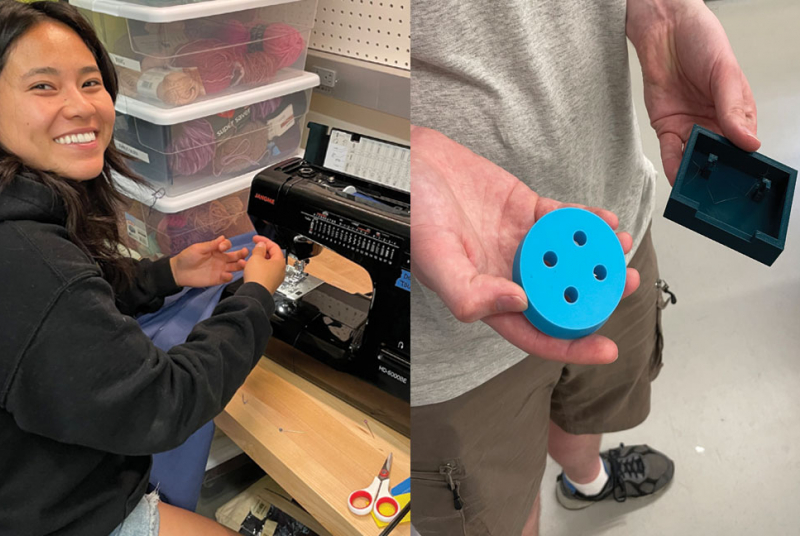
User Friendly
From the airy atrium of the new Engineering and Computer Science Center (ECSC), the towering door of the Harold Edward Cable Makerspace opens to a bright, inviting studio with long, butcher-block workstations lining the walls. A vast array of saws, clamps, and screwdrivers hang from pegboards. Sewing machines, laser cutters, and other machinery stand ready. Near a bank of computer stations, a tall whiteboard fields requests for additional supplies. Students have scrawled “matte vinyl,” “zippers,” “ball bearings (assorted bore sizes),” “jumper wires,” and “Urgent: Super Glue” on the board. A 3D printer chugs and whines in the background, disgorging an elegant, conical form. A handful of students hunch over their projects. The vibe is focused but relaxed.
This 21st-century iteration of a workshop invites anyone in the Dartmouth community to use the tech and tools for their research and class projects—or just for the hell of it. “The makerspace is co-curricular with other schools in the College, but it’s also to help entrepreneurs who may need a prototype, for example,” says Doreen Cutter, operations coordinator at the Magnuson Center for Entrepreneurship, which co-manages the makerspace with the Thayer School of Engineering.
The 1,200-square-foot studio displays a replica of an award-winning bridge designed by Anna Sandell ’23, an engineering student who was critically injured in a 2021 snowmobile accident. Her father, Scott Sandell ’86, and his family donated funds for the makerspace, which is dedicated to Anna and named for Sandell’s grandfather, Ed Cable a mechanical engineer and inventor.
“When Joe Helble, then dean of the Thayer School, convinced me that Thayer needed to expand to succeed and that a new building was needed to achieve that vision, I started to think about what I might do,” Sandell said when the shop opened in 2022. “When I saw that the plans included a makerspace, I leaped at the chance to make that space possible.”
With a budget of $20,000 per year, the makerspace serves about 200 tinkerers a week, with teaching assistants (TAs) on staff to assist during regular hours. Qualified visitors can get 24/7 card access. “We make sure there’s someone here to answer questions, and that anyone who comes in either gets help with what they need or gets referred to someone who can help,” says Chris Magoon ’13, Th’14, an engineering laboratory instructor who set up the
makerspace and has helped manage it.
He has witnessed some intriguing projects. “We’ve had folks from the medical school come in and say, ‘I’m working on this project and need a perfect 3D model of this scan of the inside of a sinus cavity.’ So we’ve got slices of a head and nose going through the printers. Or, ‘I have a perfect scan of my brain and I’d like to 3D print it.’ It’s pretty amazing.”
Across the room, computer science major Elizabeth Tatishev ’25 assembles pieces she designed and printed on a 3D printer for an assignment. “I’m taking a class called ‘Digital Fabrication and Rapid Prototyping,’ ” she says. Armed with an X-acto knife and hot-glue gun, she slices and joins the triangular chunks of gray plastic into the form of an origami-style crane. “I’m struggling with it. This is the first prototype, so it’s helping me get a sense of how the parts will interlock, which they aren’t doing now.” Tatishev designed the crane in Adobe Illustrator, exported it to a 3D modeling program, and formatted it into pieces for the 3D printer. “I have some background in the arts, so I’m taking this course to learn about technology, and interlocking design is important to working in three dimensions.”
Engineering professor Solomon Diamond ’97, Th’98, sent his students to the makerspace as part of his course on computer-aided design and kinematics. “The final project was a mechanical walking dinosaur ‘fashion show,’ ” he says. “All the custom-made mechanical components were fabricated in the Cable Makerspace.” The show featured remote-controlled dino-bots cavorting jerkily around a worktable. Students made the bots’ heads and joints from 3D-printed plastic and their legs from laser-cut plywood, along with fasteners and hardware from a kit. “The cross-fertilization of interdisciplinary learning and discovery is what makes a Dartmouth education so special,” Diamond adds. “I’ve also observed new friendships among students forming in the makerspace because hands-on learning is social and fun.”
Two TAs, including computer science major Kyrylo Bakumenko ’26, circulate to answer questions and offer guidance. Both are makerspace power users. “I came in and started doing some 3D prints, then I got trained for the laser cutter,” says Bakumenko. “Chris suggested that I become a TA here and help other students with their projects.”
Mimi Lan, Th’24, a doctoral candidate in biomedical engineering, recently fabricated a custom electronic component for her experiments. She also 3D-printed a two-foot replica of the famous Greek statue Winged Victory, which she had admired in the Louvre while in Paris for a conference. “I probably use the space at least once a week, though if I happen to be in the middle of prototyping and iterating a project, I will visit the space three or four times a week,” Lan says. “The Cable Makerspace is one of my favorite places on campus.”
Chris Quirk is a freelance writer.